

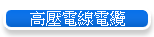
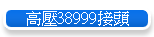
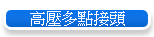
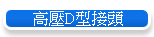
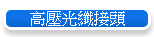
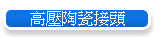
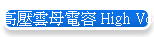
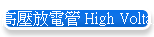
| |  Coaxial Cable
P/N 167-2896 Type“L” Inner Conductor: 19/38 strands SPC wire. AWG 26. Cable Insulation: FEP. Dia. 0.050/1.2 Shield: SPC wire. AWG 36 Jacket: FEP . Dia.: 0.095/2.4 Electrical: Voltage rating: 18 KVDC Impedance: 46 Ohms Capacitance: 28.0 PF per ft. nominal Inductance: 0.089 µH per ft.
P/N 167-2669 Type“C” Inner Conductor: 19 strands TPC. AWG 16 Cable Insulation: Clear polyethylene. Dia. 0.118/2.9 Shield: No. 36 AWG. Jacket: Polyethylene. Dia.: 0.195/4.9 Electrical: Voltage rating: 20 KVDC Impedance: 31 Ohms Capacitance: 48.0 PF per ft. nominal Inductance: 0.061 µH per ft.
P/N 167-9785 .150 Dia. FEP Inner Conductor: 19 strands SPC. AWG 20 Cable Insulation: FEP . Dia. 0.150/3.8 Shield: Single TPC braid. Coverage 90%. Dia.: 0.180/4.5 nominal Jacket: FEP. Black. Dia.: 0.220/5.5 nominal Electrical: Operating voltage: 40 KVDC Impedance: 46 ohms
RG 213/U Inner Conductor: 7 strands bare copper wire. AWG 12 Cable Insulation: Polyethylene. Dia. 0.285/7.2 Shield: Single-braid bare copper. Jacket: PVC. Black. Dia.: 0.405/10.2 Electrical: Voltage rating: 25 KVDC Impedance: 50 Ohms Capacitance: 30.8 PF per ft. nominal
Non-Shielded Wire
 P/N 178-7435 FEP .080/2.0 Dia. Conductor: 19/34 strands SPC wire. AWG 22 Cable Insulation: FEP. Color: White Electrical: Operating voltage: 22 KVDC
P/N 167-7628 FEP .100/2.5 Dia. Conductor: 19/32 strands SPC. AWG 20 Cable Insulation: FEP. Color: White Electrical: Operating voltage: 30 KVDC
P/N 167-9610 FEP .150/3.8 Dia. Conductor: 19/32 strands TPC. AWG 20 Cable Insulation: FEP Color: White Electrical: Operating voltage: 40 KVDC P/N 167-9611 FEP .180/4.5 Dia. Conductor: 19/29 strands SPC. AWG 16 Cable Insulation: FEP. Color: White Electrical: Operating voltage: 40 KVDC. Test: 50 KVDC
| Silicone Coated FEP Insulation P/N 178-8315 FEP .090/2.2 Dia. with silicone coating Conductor: 19/32 strands SPC wire. AWG 20 Cable Insulation: FEP. Color:Natural Electrical: Operating voltage: 22 KVDC
P/N 178-8781 FEP .110/2.8 Dia. with silicone coating Conductor: 19/32 strands SPC wire. AWG 20 Cable Insulation: FEP. Color: Natural Electrical: Operating voltage: 30 KVDC
Silicone Rubber Insulation Color: White. Other colors are optionalP/N 167-9634 Silicone rubber .100/2.5 Dia. Conductor: 19/32 strands SPC. AWG 20 Cable Insulation: Silicone rubber Electrical: Operating voltage: 10 KVDC
P/N 167-9193 Silicone rubber .150/3.8 Dia. Conductor: 19/30 strands SPC. AWG 18 Cable Insulation: Silicone rubber Electrical: Operating voltage: 17 KVD
P/N R790-2518 Silicone rubber .160/4.0 Dia. Conductor: 19/30 strands SPC. AWG 18 Cable Insulation: Silicone rubber Electrical: Operating voltage: 17 KVDC
P/N 178-9578 Silicone rubber .165/4.1 Dia. Conductor: 19/30 strands SPC. AWG 18 Cable Insulation: Silicone rubber Electrical: Operating voltage: 17 KVDC
P/N 167-9169 Silicone rubber .180/4.5 Dia. Conductor: 19/29 strands SPC. AWG 16 Cable Insulation: Silicone rubber Electrical: Operating voltage: 20 KVDC
P/N R790-3516 Silicone rubber .265/6.7 Dia. Conductor: 41/32 strands SPC. AWG 16 Cable Insulation: Silicone rubber Electrical: Operating voltage: 35 KVDC
P/N 167-9180 Silicone rubber .280/7.1 Dia. Conductor: 19/29 strands SPC. AWG 16 Cable Insulation: Silicone rubber Electrical: Operating voltage: 45 KVDC
P/N R790-4516 Silicone rubber .300/7.6 Dia. Conductor: 19/29 strands SPC. AWG 16 Cable Insulation: Silicone rubber Electrical: Operating voltage: 45 KVDC
P/N R790-6014 Silicone rubber .385/9.8 Dia. Conductor: 19/27 strands SPC. AWG 14 Cable Insulation: Silicone rubber Electrical: Operating voltage: 60 KVDC
Bulk cable ordering information For a complete catalog of Reynolds high voltage wire and cable products including FEP silicone coated wire and R.F. attenuation line (lossy line), contact the factory or your Reynolds representative.
|
Download this page as a PDF for best print quality. Cable preparation and assembly instructions - Series 31,310,311 Series 31 (P/N 167-0669) | Step 1 Cut cable to length, clean and square. Slip boot over cable. Strip outer jacket to dimension shown. Trim exposed braid to dimension. Trim inner insulation to dimension. No nicked or severed strands allowed.
Step 2 Insert sleeve under braid as shown. Rosin-flux and pot tin dip both the inner core and exposed braid using SN60 solder in accordance with J-STD-006. Remove all flux.
Step 3 Solder contact in place through hole using SN60 solder in accordance with J-STD-006. Completed solder joint must have a continuous fillet of solder between the conductor and the contact. The solder in the feed hole must be free of pinholes and flush or below flush. Rear of contact shoulder shall be as flush as possible with insulation of cable core, but not to exceed .030".
Step 4 Slip prepared cable into the connector body until the flange inside the connector butts against braid cut off. Solder connector body to braid through 4 holes using SN60 solder in accordance with J-STD-006. Clean thoroughly.
Step 5 Slide boot into position as shown. | | Series 310 (P/N 167-4356) | Series 311 (P/N 167-7624-1, -2, -3) | Step 1 Cut cable to length, clean and square. Slip boot and crimp sleeve over cable. Strip outer jacket to dimension shown. Trim exposed braid to dimension. Trim inner insulation to dimension. No nicked or severed strands allowed. Pot tin dip inner conductor using SN60 solder in accordance with J-STD-006. Remove all flux.
Step 2 Solder contact in place through hole using SN60 solder in accordance with J-STD-006. No solder buildup allowed on contact outer diameter. Completed solder joint must have a continuous fillet of solder between the inner conductor and the contact. The solder in the feed hole must be free of pinholes and flush or below flush. Rear of contact shoulder shall be as flush as possible with insulation of cable core, but not to exceed .030". Flair braid by moving cable core in a circular motion.
Step 3 Insert prepared cable into connector assembly. When contact shoulder butts against flange of insulator, slide crimp sleeve over braid and connector. Trim excess braid and crimp using Thomas & Betts crimping tool No. WT308 or WT408 or an equivalent crimp tool. Slide boot in place | 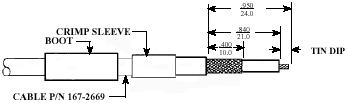
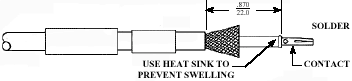

| Download this page as a PDF for best print quality. |
Cable preparation and assembly instructions - Series 521
Download this page as a PDF for best print quality. Cable preparation and assembly instructions - Series 600, 610
Download this page as a PDF for best print quality. Cable preparation and assembly instructions, Series 730/830, 737
Download this page as a PDF for best print quality. Cable preparation and assembly instructions, Series 730/830, 737 w/ Silicone Coated FEP Cable & Nomex Jacket
Download this page as a PDF for best print quality. Cable preparation and assembly instructions, Series 720, 727
Download this page as a PDF for best print quality. |